-
Nutrivend selects Forterro’s Orderwise to support online expansion and streamline operations - April 11, 2025
-
Breaking down the automation cost barriers - April 11, 2025
-
ARROWXL LAUNCHES AMBITIOUS ZERO WASTE ROADMAP - April 8, 2025
-
THE BCMPA’S NEW CAMPAIGN DRIVES OUTSOURCING SUCCESS IN Q1 - April 7, 2025
-
‘Solution Agnostic’ approach to automation brings warehouse agility - April 2, 2025
-
BITO supports Tomorrow’s Warehouse - April 1, 2025
-
BLACKOUT TECHNOLOGIES TARGETS TELEMATICS-INTEGRATED MOBILE DEVICE BLOCKING TO COMBAT SMARTPHONE DISTRACTION - April 1, 2025
-
Balloon One to enhance stock visibility for Moonpig with new WMS - March 27, 2025
-
OpenADR Alliance announces first OpenADR 3.0 certified products with EVoke Systems, E.ON Energy and Universal Devices - March 25, 2025
-
Growing fulfilment and contract packer appoints new Managing Director - March 25, 2025
Frazer Watson, UK – Ireland Country Manager at AMR designer and manufacturer iFollow, examines the quality differentiator when it comes to choosing an Autonomous Mobile Robot solution.
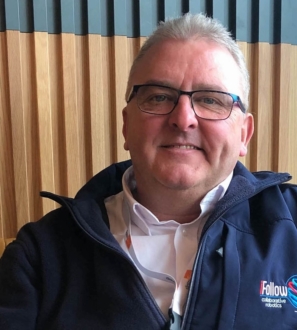
Autonomous Mobile Robots (AMRs) are rapidly building a reputation for being a smart, flexible and productive intralogistics transport solution. At a time of increasingly scarce labour, AMRs can be deployed to work in cooperation with staff, enabling manufacturing, warehouse, fulfilment and distribution centre operations to redeploy personnel resources from simple transport duties to where they can be most productive – such as picking orders into roll cages or onto pallets being carried by the robots.
These facilities are often demanding environments for materials handling equipment. The surfaces on which AMRs travel are not always the smoothest and they are often full of static obstructions such as racking, shelving, conveyors as well as mobile ones like forklift trucks. Mobile robots can rack up significant mileages through a typical year in these environments, working long shifts carrying loads up to the unit’s capacity.
The combination of these factors is why, like any item of materials handling equipment, quality build and robustness are vital characteristics for an AMR – not only to ensure a longer lifespan for the unit, but also to minimise downtime due to repairs.
There and numerous predictions for AMR market growth through the coming decade and while there are many lower cost units that will have limited uses, market growth will be boosted as the limitations that preclude many units from broader applications are being overcome by higher quality mobile robots, such as those from iFollow.
Increased payload capabilities up to 1.3 tonnes will give mobile robots the potential to carry out tasks such as moving barrels or pallets of paint cans. This is just one example of how improving AMR capabilities will broaden their possible deployment. The ability to work between different temperatures, which can risk strain on internal components, is another. Moving between temperature zones from as cold as -25°C to as warm as +40°C, in constrained environments, presents more of a challenge for mobile robot technology than many may realise. In iFollow mobile robots, for example, the temperatures of the key electronic components are regulated by a servo system completely developed by our teams. Thus, the absence of condensation is ensured, even when moving from a very cold environment to a temperate space.
As the number of mobile robot brands and models available on the market increases customer choice, the quality of the design and build is set to be a crucial differentiator. While many mobile robots look similar on the outside there remains a great deal of difference when it comes to quality. And this should be a prime consideration when choosing the right model for applications in which the AMR is to be deployed. The long-term success of an operation will depend on the AMR having the reliability and capability to maximise uptime and maintain flow through a warehouse or production facility.
Check that the AMR has all the required registration and certification. Buying a fleet of a couple of hundred mobile robots, for example, without certification is a huge risk. Has the machine been through a quality process? Is it CE certified? Does it meet the latest standards that are in force for the region where it is being used? What about support – can parts be supplied locally for quick response?
A supplier that both designs and manufactures its own AMRs, as well as providing the supporting software, can better respond to customer problems with solutions adapted to their particular needs. It will be able to tune the mobile robot solution to the application – for example adapting the lifting platform to the needs of the application. This ability often allows a supplier to adapt a single type of robot to fulfil a customer’s entire needs.
iFollow operates in the food, industrial, pharmaceutical, chemical, cosmetic, logistics and mass distribution sectors, which all operate busy, fast moving facilities. The company made the strategic choice to design and manufacture its own autonomous mobile robots – which are all guaranteed – and fully develops its own navigation and fleet management algorithms. Mobile robots are a relatively new technology that is rapidly gaining momentum as a means to gain competitive edge – from grocery retail logistics to industrial manufacturing. Seeking out premium machines that are designed for use in intense, constrained environments and repeated use over time will ultimately deliver greater value for the end user.